Our industrial resources
Vitalac, based in Carnoët in Brittany, has very high-performance industrial resources, providing top-quality to local farmers, distributors or industrial clients around the world.
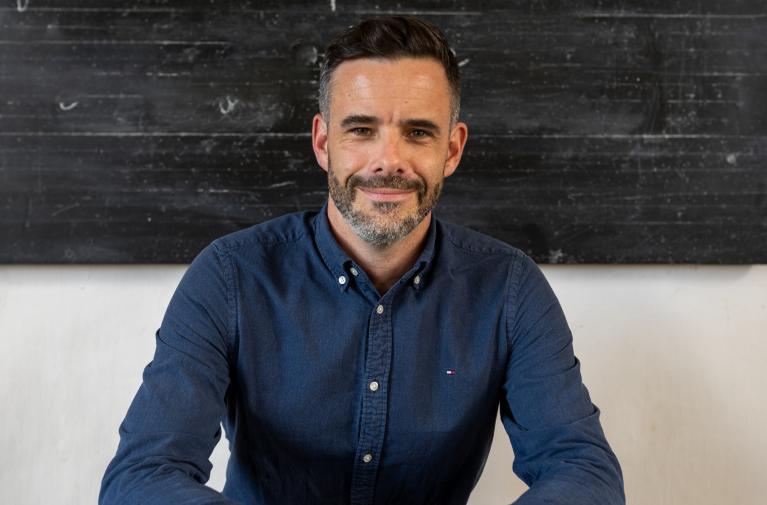
We are fortunate to have high-quality teams that match the pace of our industrial tool.

We had 2 packaging lines in 2003 and we now have 8 today, we went from one mixing line in 2013 to 6 today and we have tripled our production area from 5 to 15,000 m2.
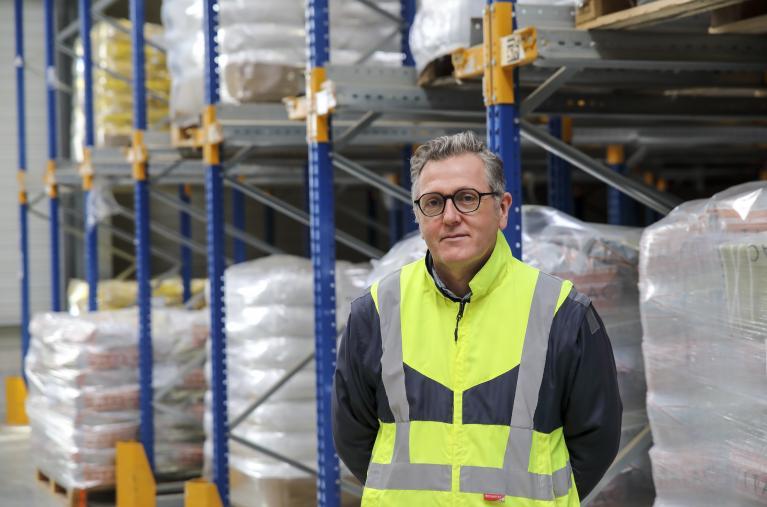
Manufacturing safety, high-quality products and regular investments make Vitalac a reliable company with forward-looking projects.
A dynamic industrial investment policy
In Carnoët, in Brittany, the historic headquarters of Vitalac, we have a state-of-the-art, very modern industrial tool, in which the company has always invested. In constant evolution, we are continually adapting to market needs. Our industrial resources have expanded along with this growth and investments are made every year to improve both productivity and efficiency.
"Vitalac has been able to invest in the right activity at the right time." Gaylord Thafournel, Industrial Manager. Vitalac’s policy is to continually improve equipment, processes, automation equipment, buildings, production and storage units.
In 2016, the company invested 8 million Euros to modernise the warehouses for raw materials and finished products as well as to create unit 2, dedicated to liquids and powders. Thanks to this dynamic investment policy, Vitalac benefits from an ultra-modern tool that sets the standard with regards to organisation. Vitalac’s 2021-2023 investment plan, supported by the stimulus package, is 4 million Euros.
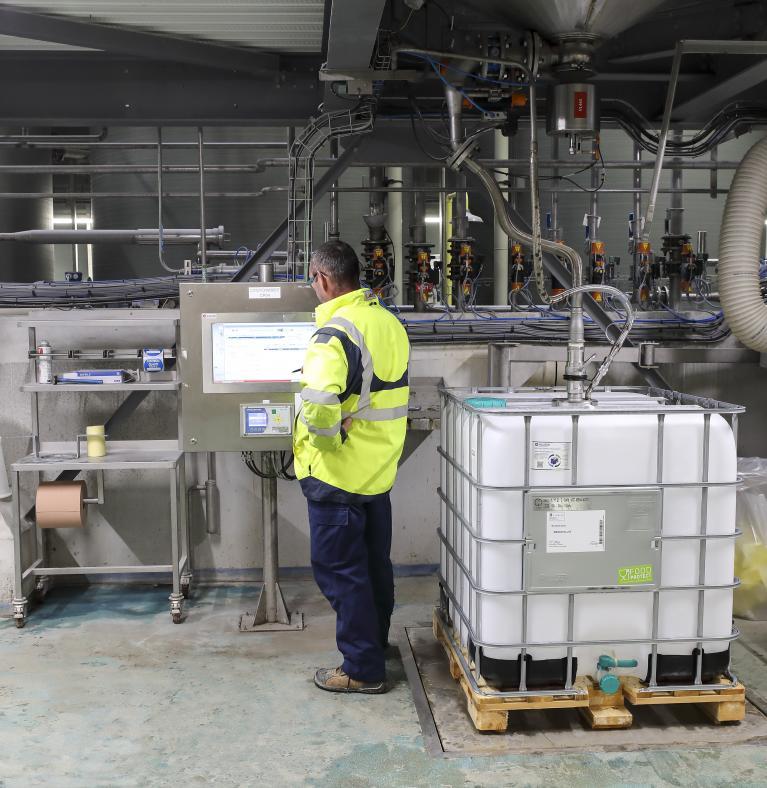
Materials are transported by a dense phase pneumatic conveyor system; this is a major advantage because it allows to avoid any cross-contamination, unlike mechanical conveying. Compressed air is used to convey the product. Dry and filtered air that meets food quality standards. In the animal nutrition sector, not many manufacturers use this technology. On the packaging side, Vitalac is very well equipped with an automated system and a dedicated computer system, allowing control and monitoring of its production process.
“We have very high-level technical resources, which means we can provide top-quality to local farmers, distributors or industrial customers around the world.” Gilbert Le Calvez, CEO.
The strength of Vitalac is that it is able to manufacture a very broad range of products, from premixes to complete feed while including nutritional products. We can be highly flexible with regards to presentation - liquid, powder, granule, crumb, pellet forms - and packaging - from small formats to bulk. This wide diversity must be based on fail-safe organisation and thoroughness.
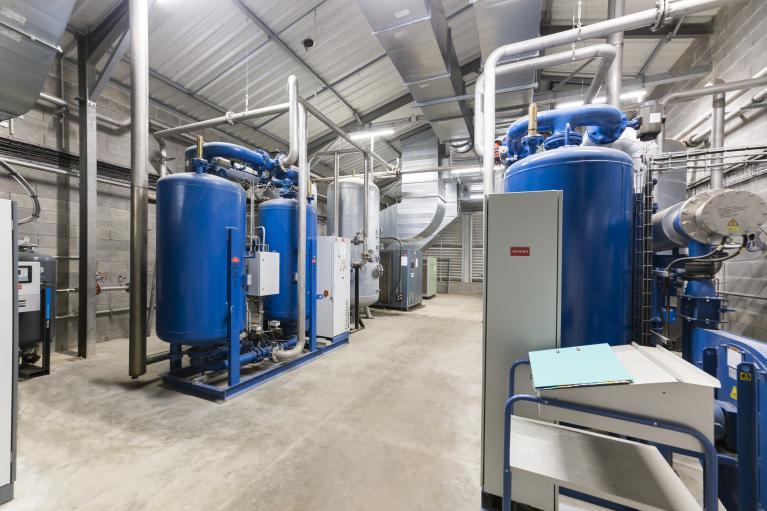
An appropriate in-house analysis laboratory
We have invested in an in-house laboratory that enables us to be highly reactive so that we can fulfil three missions:
- ensure our quality control plan
- support the innovation and development of our products
- provide our customers with an analysis service for personalised advice
Our teams perform physical-chemical, biochemical or bacteriological studies on a daily basis. This represents a continuous investment in advanced equipment, such as XRF-fluorescence which measures mineral micro- and macronutrients or our Near Infrared device which analyses everything that is organic (protein, starch, fat).
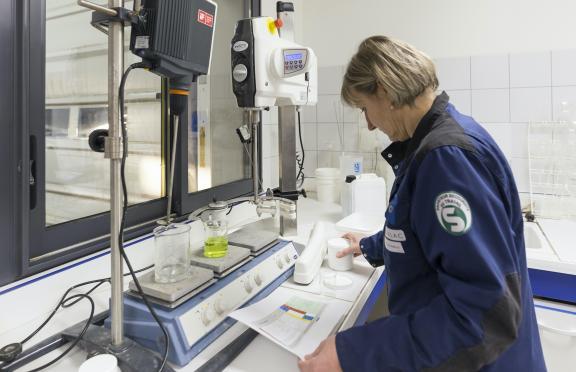
A fully automated and computerised system
In 2017, Vitalac implemented a new information system that allows us to have control over the entire chain at all times: to enter orders, to make quotes, to plan, buy and manage product stocks and entries, to ensure safety and efficiency as well as a better flow of information internally. And we will carry on with the switch to a paperless system so that we continue to save time with digitalisation.
As all these steps are controlled in-house, Vitalac has optimised its logistics and has demonstrated its high responsiveness in serving its customers in France and around the world. The site is entirely safe and automated, providing full traceability and reproducibility. Thanks to our information system, we are able to guarantee the complete traceability of all our products. Working with over 400 different raw materials, the company leaves nothing to chance with a real-time location-based inventory management system (IMS). As soon any material is moved, its bar code is scanned so that it can be fully tracked. Its traceability and inventory management system positions Vitalac as one of the leaders in animal nutrition manufacturers.
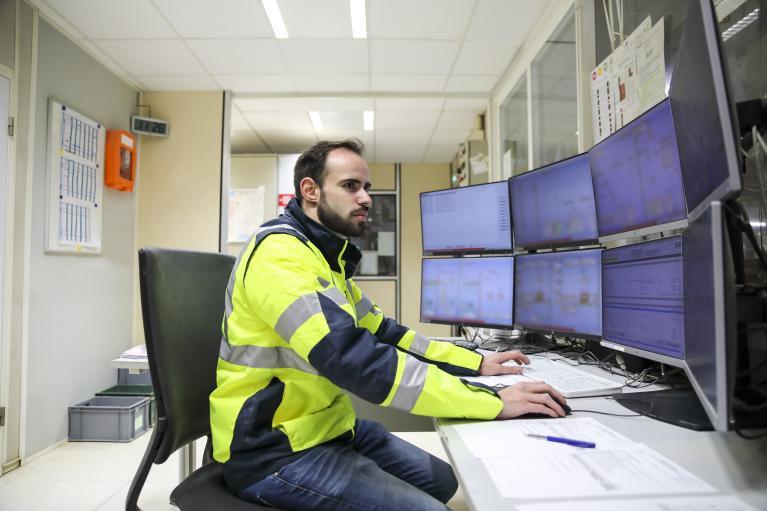
An established QHSE approach
At Vitalac, we have a dedicated Quality and Health/Safety/Environment (HSE) department which monitors the quality of our products, the safety of both our employees and our processes and even compliance with regulations.
From the moment when raw materials arrive on our site up to the final use of our products by our customers, everything is controlled. Samples are taken throughout the chain and analysed in our own laboratory. These analyses ensure the compliance of the incoming raw materials, the homogeneity of the finished products and the absence of contamination; all these criteria guarantee optimal quality and safety.
This requirement level is validated by obtaining all the certifications linked to our profession, such as the OQUALIM and FAMI QS standards, as well as by monitoring the satisfaction of our customers, something that is a key indicator for us. We are in a HACCP system with an annual audit.
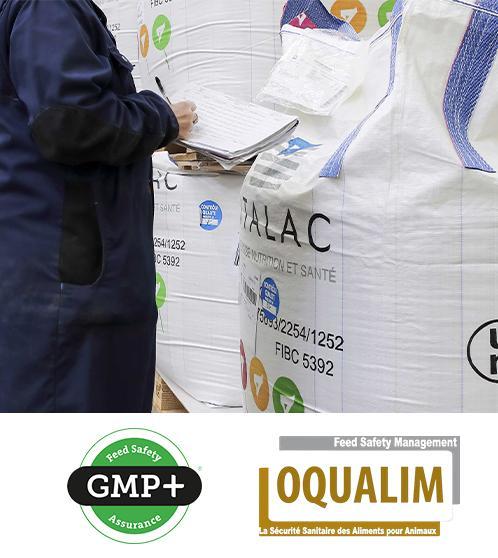
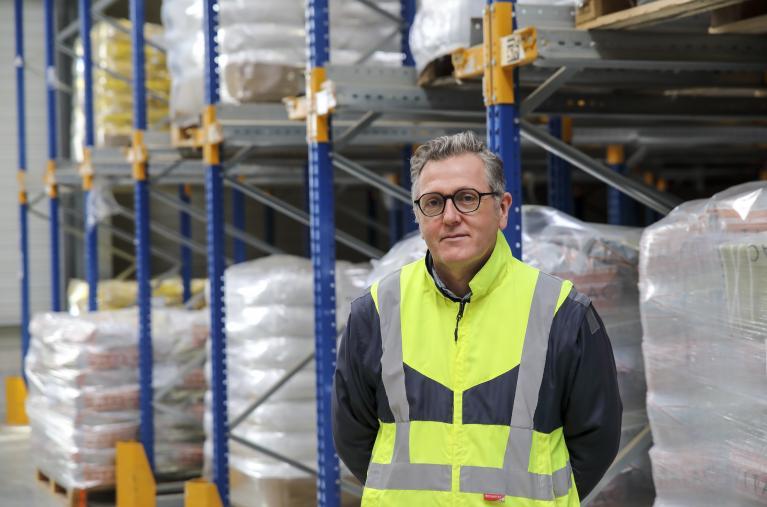
We have recruited someone whose specific role is to oversee and develop our HSE policy. HSE topics are essential and are a priority at Vitalac. For example, one important objective in the upcoming months is to improve our waste management by working on the channels, recycling, the suppliers taking back what? and consumable recycling on farms.